We start out this installment with new electronics being installed.
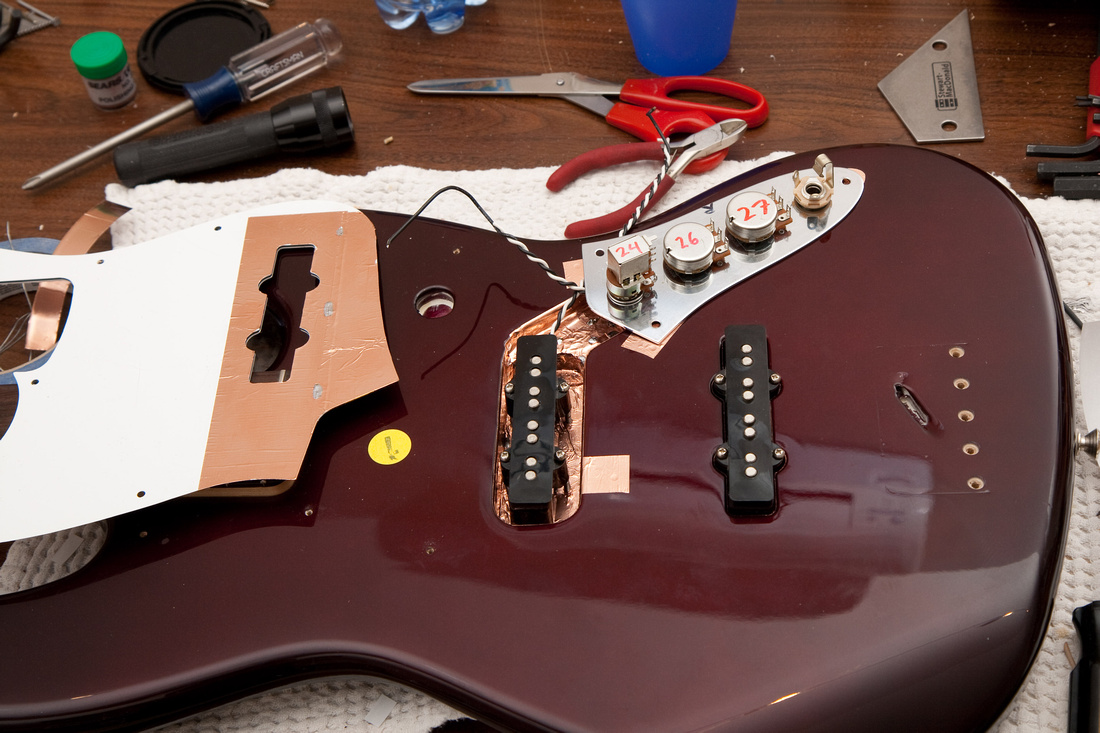
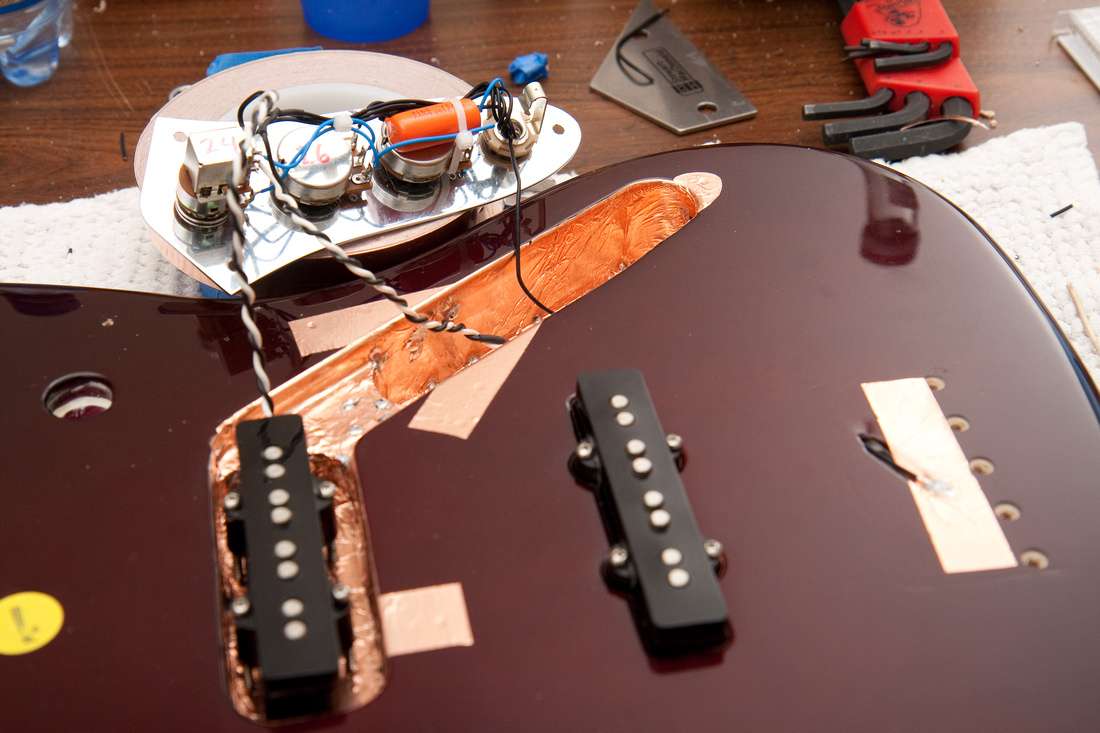
And this operation is almost done. . . ready to close it up. One more detail. . . I don't know why I didn't think to do this before as it's a lot cleaner than crushing wire under the bridge.
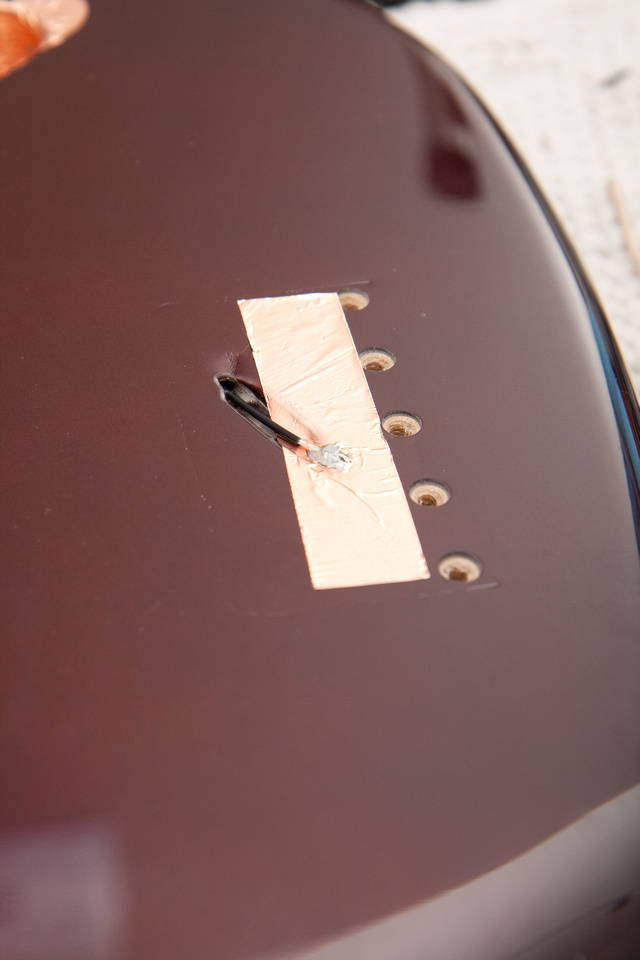
The nut slots were a bit high on the G and D strings, so I brought out my little Norman nut slots files for the first time to give 'em a little zap. Nice and easy on these. A little cutting goes a long way.
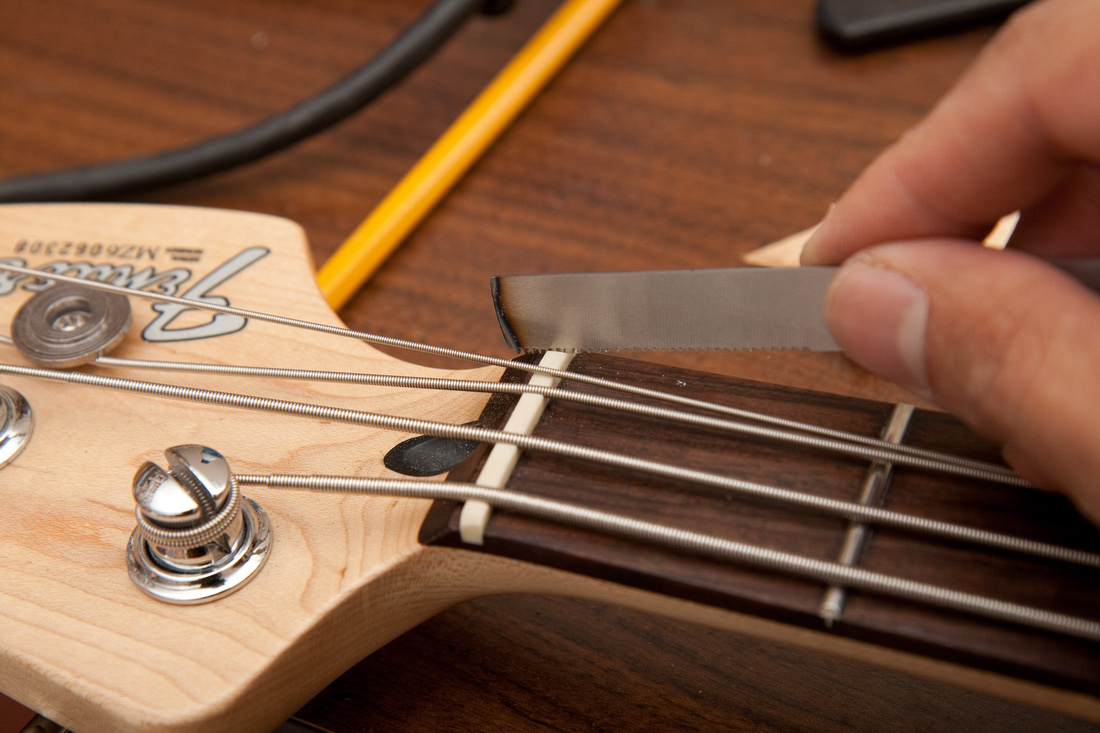
As I was setting this bass up, I noticed 2 things. . . one, this was just about the most un-inspiring instrument I have ever played. . . I knew the strings on there were pretty new so I had a little argument with myself about how the cost is already high and how it would be a waste of a "good" set of strings. . . blah blah blah. I finally decided to just swap out the strings (D'addario nickel round wounds). I've never been a fan of nickel strings, and no offense to people who like them, but this particular set on this bass sounded beyond mediocre. . . just downright uninspired tone. I plan to do some testing with the bass, and I'd just be wasting precious studio time if I left the strings as they were as it would be a string comparison as opposed to a bass comparison. In order to get good data, I had to swap 'em out.
I was also getting fret buzz along a large portion of the neck again. . .not isolated to one fret. . . large areas. . . I took my notched straight edge out and figured something out. I knew I needed to cut more fall-off because the buzz was coming from the last couple of frets and since this neck was so straight and the Fender frets are small, I didn't want to cut too much fall-off. It didn't make any sense to me why on all of the basses, I needed to cut so much fall-off. Most people talk about creating a few thousandths of "un-noticeable" fall off, but I'm hacking off huge chunks on all of these builds. The straight edge under string tension revealed a hump starting around the 15th fret extending to the 20th fret (right where I typically cut my fall-off. . . to the 15th fret). So, in effect, I'm not really creating fall-off but under string tension, I'm flattening out the fretboard because the truss rod does not pull evenly all across the neck. I'm now starting to really think about a neck jig because I would be able to compensate for the hump much more precisely when I'm doing the initial level. So, I learned that conditions on a loose neck and conditions under string tension are very different. By trial and error, I had figured out a way to compensate for the problem in my setups without actually identifying it until now. At any rate, 3 layers of blue painters tape on the 11th fret. . . I cut my fall-off to the 15th fret (where the hump begins). And then, of course, crown and polish those frets. . . .. . again . . . .

And the setup is now sweet. . . the new strings sounded great. . . in fact, that's one of the really nice things I've discovered in these builds. It thought initially that these Stainless Steel Dunlops would be a great "budget string". . . but I have discovered that these are just fantastic sounding strings all around. As of right now, I think these are on par or better than any other high dollar string out there. . . seriously. What a find. The bass really came alive after the string change. I put a couple of black Fender knobs on so the set is not mis-matched anymore, and #5 is DONE!!!
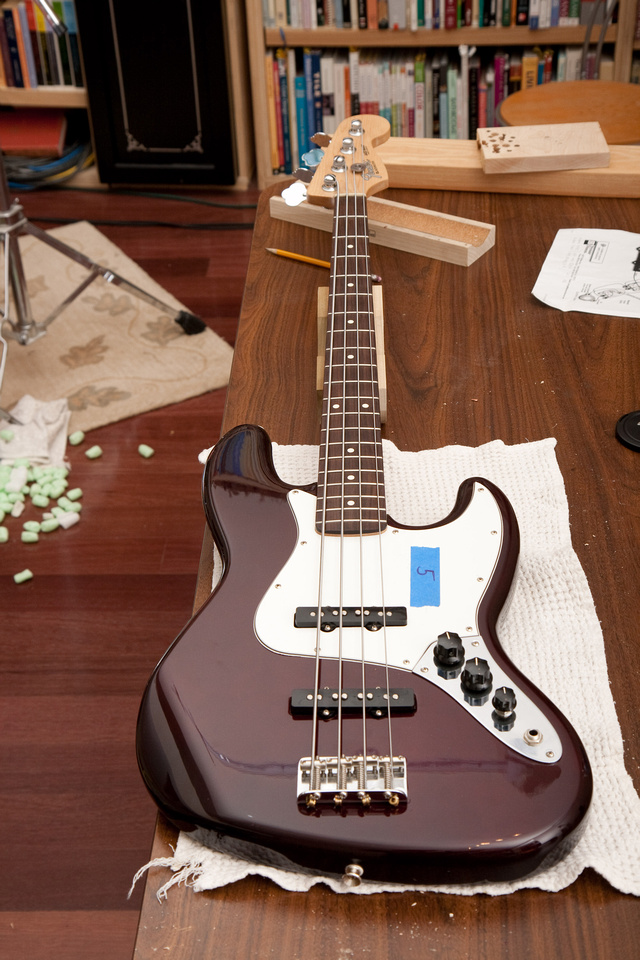
No comments:
Post a Comment